Prof. Dr.-Ing. Stefan Soter
Kontakt:
Rainer-Gruenter-Str. 21
42119 Wuppertal
Raum: FH.01.07
Stefan.Soter[at]uni-wuppertal.de
+49 202 439 1950
Termine oder Anfragen bitte über mein
Sekretariat
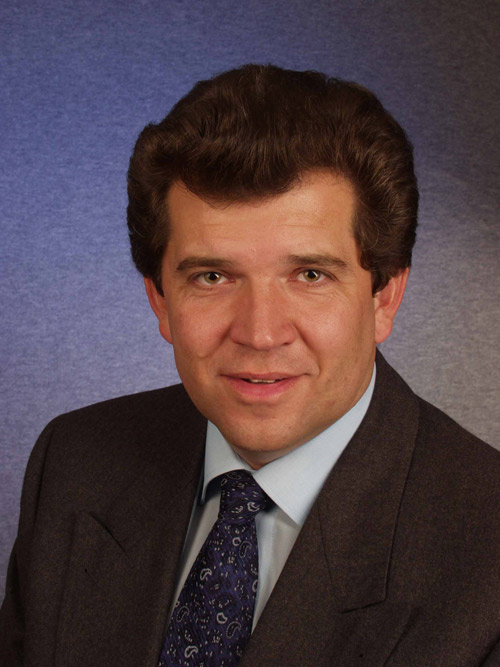
Persönlicher Werdegang
- 10/1984 bis 11/1989 Universität Bochum; Abschluß: Dipl.-Ing. Elektrotechnik
- 01/1990 bis 04/1996 FernUniversität Hagen Institut Solatec (Prof. Dr.-Ing. D. Hackstein)
- 01/1994 Promotion zum Dr.-Ing der Elektrotechnik
- Thema der Dissertation: "Systemtechnik für photovoltaisch gespeiste Asynchronmaschinen zum Antrieb von Wasserpumpen"
- 05/1996 bis 03/2007 Technische Universität Dortmund (Prof. Dr.-Ing. Dr.-Ing. S. Kulig) Lehrstuhl für Elektrische Antriebe und Mechatronik, vormals Lehrstuhl für Elektrische Maschinen, Antriebe und Leistungselektronik
- wissenschaftlicher Assistent, Oberingenieur (ab 07/1997), Akademischer Rat (ab 03/2001), Akademischer Oberrat (ab 03/2004)
- seit 04/2007 freiberuflicher Leiter von Industrieprojekten in Kooperation mit der Bergischen Universität Wuppertal, Lehrstuhl für Elektrische Maschinen und Antriebe, Prof. Dr.-Ing. Ralph Kennel
- 04/2005 Angebot der W3-Vertretungsprofessur "Leistungselektronik" der Helmut-Schmidt-Universität Hamburg
- ab 10/2008 Lehrauftrag an der Rheinisch-Westfälischen Technischen Hochschule Aachen (RWTH) (Prof. Dr.-Ing. Dr. h.c. dr hab. Kay Hameyer) Institut für Elektrische Maschinen. Titel der Vorlesung: Aufbau und Netzbetrieb von Windkraftanlagen
- 10/2008 bis 02/2010 W3-Vertretungsprofessur für "Elektrische Maschinen und Antriebe" der Bergischen Universität Wuppertal
- ab 03/2010 W3-Professur für "Elektrische Maschinen und Antriebe" der Bergischen Universität Wuppertal
Vorlesungen
- Grundlagen der Elektrotechnik III
- Geregelte elektrische Antriebe
- Leistungselektronik
- Windkraftanlagen
Veröffentlichungen
- 47.T. Rösmann and S. Soter, "Mechanically commutated self control of PM- synchronous machines" in 2011 IEEE Energy Conversion Congress and Exposition, 2011, pp. 1555--1559.
Abstract:
In this paper a new method and device is presented that enables a PM-motor to be directly powered with an electrical DC backup source. The presented method uses discrete voltage vectors for motor control as they are well known from Direct Torque Control and Direct Self Control (DSC). The most distinctive difference of the presented method is that it works via a mechanical commutator device without any micro- or power electronics. In opposition to DTC and DSC where flux and torque are controlling the selection of voltage states, the presented method uses the mechanical rotor position to control the discrete voltage vectors. Based on that, the presented method is called MCSC, which means mechanically commutated self control. A simple and robust construction of the commutation device guarantees a low failure probability and the possible integration into the motor housing. Only in emergency case the commutator is activated for a short period of time in order to move the motor into a safe position, stopped with limit switches. Therefore the device can be designed for motors lifetime although carbon brushes are used and a regular maintenance is not necessary as it is known from brushed DC machines. - 46.S. Gruber, C. Junge, R. Wegener and S. Soter, "Overview of a special Developed Linear Drive Concept with integrated Hydraulic Cylinder für Clutch-Brake-Combinations in Eccentric Presses" in Proceedings / LDIA 2011, the Eighth Symposium on Linear Drives for Industry Applications, July 3 - 6, 2011, Eindhoven, The Netherlands, Eindhoven: {TU Eindhoven}, 2011.
ISBN: 978-90-386-2524-9
- 45.C. Prasse, A. Kamagaew, S. Gruber, K. Kalischewski, S. Soter and M. Hompel, "Survey on energy efficiency measurements in heterogenous facility logistics systems" in 2011 IEEE International Conference on Industrial Engineering and Engineering Management, 2011, pp. 1140--1144.
ISBN: 2157-362X
Abstract:
Basically there are two ways to improve the energy efficiency of heterogeneous material flow systems - modification of technical components and control with intelligent strategies. In order to reduce the consumed energy the design, configuration and control strategy of different conveyor systems have to be analyzed by mechanical and electrical measurements. To quantify the need of energy under conditions as close as possible to reality a testing facility with different conveyor elements and electrical drives with power monitoring capabilities was installed in order to give a database for further research activities. On the one hand the acquired data can be used to optimize the efficiency of the total drive train. On the other hand they conduce to develop new intelligent control strategies for an energy efficient operation of heterogeneous facility logistics system. Eventually, the design of a monitoring system in a testing facility is the topic of this contribution. - 44.R. Wegener, K. Nötzold, A. Uphues, R. Griessel and S. Soter, "Test bench for multi-MW grid side wind power converter" in 2011 IEEE AFRICON, 2011, pp. 1--5.
Abstract:
This paper deals with an integrated full power test bench for the grid side of a wind power converter. The speciality is the high side voltage and current measurement to use the stray inductance as an additional filter element. The presented test bench is enhanced for fault ride through measurement capabilities with a full power grid simulator. - 43.F. Senicar, C. Junge, S. Gruber and S. Soter, "Zero sequence current elimination for dual-inverter fed machines with open-end windings" in IECON 2010 - 36th Annual Conference of the IEEE Industrial Electronics Society, 2010, pp. 853--856.
ISBN: 1553-572X
Abstract:
A dual-inverter allows to increase easily the maximum available power of a given inverter. When connecting two equal inverters to a machine with open end windings, the available power will raise by factor $\surd$3. However, the dual inverter also introduces a new degree of freedom for the current, which is the zero component current. The dual inverter is known for developing zero component currents, which have three times the frequency of the fundamental current, and can be of a rather large amplitude. This paper analyses the origin of these zero component currents and shows an example of how to eliminate them. Moreover it shows the possibility to suppress zero component currents by using only software algorithms modifying the current control loop. There is no need for extra components. Moreover there are no drawbacks in the quality of control as well as regarding the maximum available voltage. - 42.A. Bartsch, S. Gruber, R. Wegener and S. Soter, "Testbench for electrical drive systems in hybrid applications" in 2010 IEEE International Conference on Industrial Technology, 2010, pp. 1136--1140.
Abstract:
This paper deals with the development of a test bench for mild hybrid drives used in construction machines. Due to the special conditions under which construction machines are operating this test bench needs to be adapted. Hence the bearing of the electrical drive, which is mounted directly to the internal combustion engine, the temperature control by a cooling circuit and the integration of an appropriate inverter as well as an electrical drive to complete the system are defining the specific requirements of the test bench. These circumstances also affect the measurements and have to be considered during the evaluation of the results. - 41.C. Junge, S. Gruber, F. Budschun and S. Soter, "System analysis and optimization of a pressure control for a hydraulic-Clutch-Brake-Combination actuated with a linear drive" in 2010 IEEE International Conference on Industrial Technology, 2010, pp. 427--432.
Abstract:
This paper deals with the analysis of an electro-hydraulic system and conception of a pressure control. The controlled system consists of a permanet magnet linear actuator, a hydraulic pressure line and a Clutch-Break-Combination (CBC). The linear actuator generates a force which causes the pressure in the hydraulic line. Depending on the system-pressure, the Clutch-Brake-Combination brakes or clutches with a different torque. Because of the integrated prestressed springs of the CBC, the controlled system is very nonlinear. In addition there are different disturbances, which makes it hardly controllable. The linear actuator is driven with a standard inverter. - 40.C. Junge, J. Gallep, R. Wegener and S. Soter, "Simulation and verification of an eccentric press system actuated by hyraulic-clutch-brake-combination controlled by a linear drive" in 2010 IEEE Region 8 International Conference on Computational Technologies in Electrical and Electronics Engineering (SIBIRCON), 2010, pp. 800--805.
Abstract:
This paper deals with a Matlab/Simulink-Simulation of an eccentric press with an hydraulic Clutch-Brake-Combination (CBC) and the verification on a standard moulding press. The outstanding characteristic of this system is the special control of the CBC. A servo converter controlled linear drive with an integrated hydraulic cylinder generates the pressure for the CBC. A developed pressure control is able to control the torque of the CBC and therefore the acceleration and deceleration of the powertrain. The simulation has been made to predict the behavior of the controlled CBC in an eccentric press. The simulation results are finally compared with the measurements at the real system. - 39.S. Gruber, C. Junge, R. Wegener and S. Soter, "Reduction of detent force caused by the end effect of a high thrust tubular PMLSM using a genetic algorithm and FEM" in IECON 2010 - 36th Annual Conference of the IEEE Industrial Electronics Society, 2010, pp. 968--973.
ISBN: 1553-572X
Abstract:
In order to meet industrial safety standards in eccentric presses, the detent force of the acting high force tubular permanent magnet linear synchronous machines (PMLSM) should be reduced. The detent force is caused by two components: the slot effect and the end effect. Both effects are based on the reluctance change between permanent magnet (PM) and stator teeth. The slot effect is already optimized by the closing slot technique which is proven by measurements presented in this paper. The main topic is the reduction of detent force by using auxiliary poles at the end of the machine. Therefore a special genetic algorithm (GA) is developed which rates the simulation results of the FEM and produces new auxiliary poles. The combined simulation tries to find an optimal size and position for auxiliary poles to reduce the whole detent force. The numerical calculations propose a minimized detent force caused by the located poles, which is independent from the length of the machines (2, 3 or 5 modules). - 38.K. Nötzold, A. Uphues, R. Wegener and S. Soter, "Highly integrated inverter with multiturn encoder and software-based PFC for low cost applications" in 2010 IEEE International Conference on Industrial Technology, 2010, pp. 764--768.
Abstract:
Motor control gets more and more common in fields where it was not applicable a few years ago. The prizes for computing power due to higher integration of the power electronics are going down. Because of this, brush-less DC and permanent magnet synchronous machines capture new markets and replace simple grid connected induction machines. The rising standards for electromagnetic interference (EMI) emissions make a power factor correction (PFC) in a lot of applications necessary. In addition a PFC offers some advantages because of the DC bus regulation. In this paper an inverter with a particularly low prize and a high performance is presented. A software based PFC is integrated into the motor control circuit and a low cost absolute position encoder has been developed. In addition some synergetic effect between motor control and PFC will be shown. The experimental results show the feasibility of the integration of a field orientated control with an integrated PFC in one low cost microcontroller.